The controller is one of the essential parts of any CNC, laser, or 3D printer. If you don’t want to buy industrial controllers, you have two choices: you can either turn an Arduino board into a CNC controller or turn a computer into a CNC controller.
Arduino-based controllers use firmware such as GRBL inside a dedicated CNC controller, whereas Mach3 (or Mach4) or LinuxCNC are control software for computers.
But when it comes to GRBL vs Mach3, which is best?
Personally, I prefer GRBL Arduino controllers over computer-as-controller Mach 3 systems, because GRBL is easier and more beginner-friendly.
However, you may decide Mach is better for you if want to control a CNC with a rotary axis, or simply don’t know how to build a G2Core controller.
(Don’t worry – if you don’t know how to build an Arduino-based controller, we have prepared a complete tutorial for you in other articles).
In this guide, I’ll compare the strengths and limitations of my hands-on experience with the two CNC control methods so you can decide which is right for you.
Hardware Differences: Mach vs GRBL
The Boards
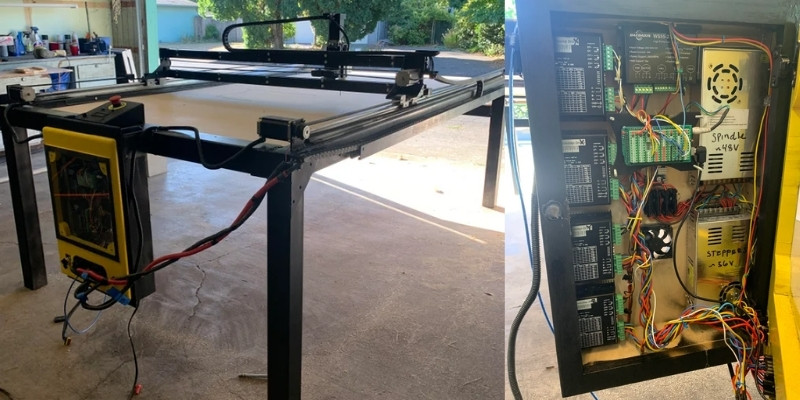
All Arduino CNC controllers like GRBL have the same arrangement as industrial controllers: they use a microcontroller, which is like a mini-computer. Arduino boards have many pins for different control tasks.
Mach3 (Mach4) and LinuxCNC use your computer’s motherboard and its parallel port to access it.
In this method, you have to buy an external motion device or a breakout board (BOB) for the following two reasons:
- Computer manufacturers have eliminated parallel ports, so you need external motion devices to extend pins from your computer’s USB or ethernet.
- Even if your computer has a parallel port, you have to isolate your computer’s motherboard from possible electrical current surges and extend its pins for wiring. Since your computer is expensive and has become a part of your CNC hardware, you have to buy BOBs that have optoisolators (optocouplers).
If you need a BOB for your parallel port, here is a nice and cheap one on Amazon. It protects your computer with optocouplers and extends your parallel port’s pins even for a 5-axis CNC. Plus, you can power it with a USB cable.
But if you don’t have a parallel port and need a BOB to operate from your USB, here is a cheap board on Amazon that supports 4-axis. You can power it up with 24v to isolate and protect your computer’s USB and motherboard.
Lastly, Arduino CNC shields help you to skip a lot of wiring if you choose Arduino controllers. This is especially useful for lasers, 3D printers, and small CNCs that use GRBL.
GRBL vs Mach: Dedicated Controller vs Dedicated Laptop
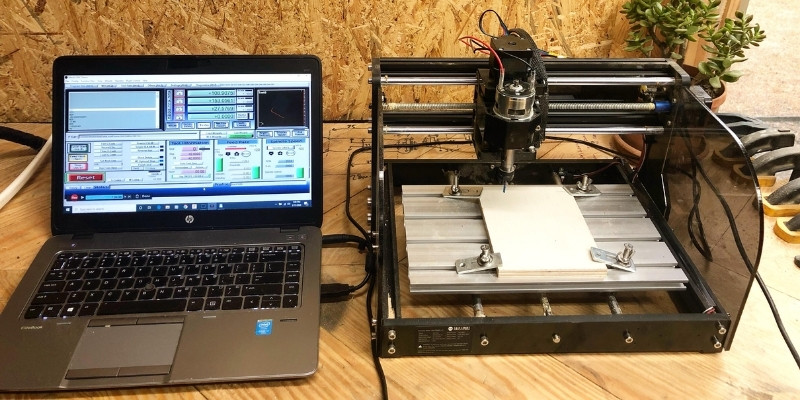
Your CNC, laser, or 3D printer is a complete machine with a dedicated controller like GRBL. You can connect to it with any computer and send G codes.
But if you have bought Mach3, only the laptop with this control software can connect to your CNC and become a part of its hardware.
I find parallel porting to be somewhat unnatural for this very reason.
Human Machine Interface (HMI)
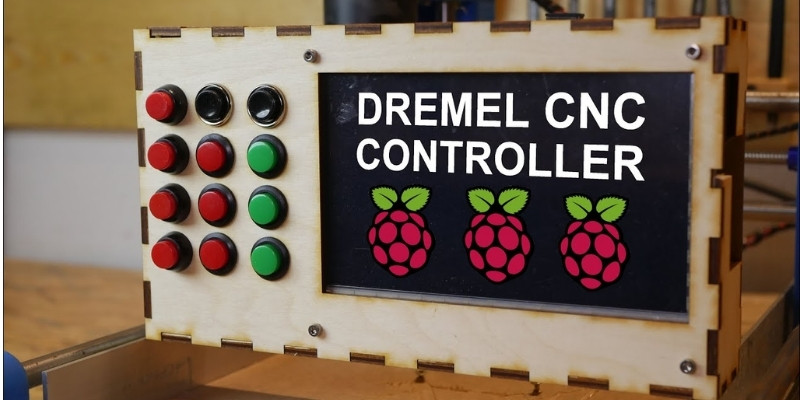
You can run GRBL with a Raspberry Pi. This gives you the ability to use touchscreens to control a CNC. However, you don’t get this cool feature with Mach3.
The Key Comparison Points for GRBL vs Mach
Price
GRBL and G2Core are free firmware and we have explained how to make a CNC controller with them. Regarding their hardware, you need an Arduino and possibly a CNC shield. These are very cheap.
With parallel porting, you can use LinuxCNC for free or buy Mach3 (or Mach4) for a couple of hundred dollars (Mach3 is $175 at the moment). If we put its dedicated laptop aside, you will also need a BOB with optoisolators (we recommended two great cheap options earlier in this article).
Winner: Using LinuxCNC with BOBs or Arduinos is cheap while using Mach3 (or Mach4) is considerably more expensive.
Software | Price |
---|---|
Mach3 | $175 |
GRBL | Free |
Control Software Differences
If you have turned your computer into a CNC controller, Mach3 (Mach 4) and LinuxCNC are your only options for control software.
Plus, since a lot of people are not comfortable with Linux, buying Mach3 (Mach4) is their only choice and they have to stick with it forever.
On the other hand, since GRBL is a popular dedicated controller, you can choose between a variety of control software: UGS, ChiliPeppr, OpenBuilds Control, Carbide Motion, Easel, Coolterm, CNCjs, and more can interact with GRBL.
Winner: GRBL has more options
Software | Control Software |
---|---|
Mach3 | Limited |
GRBL | More options such as: UGS, ChiliPeppr, OpenBuilds Control, Carbide Motion, Easel, Coolterm, CNCjs, and more can interact with GRBL |
Read more:
Ease of Use, Learning Curve, and User Interface
As we mentioned, GRBL enjoys an abundance of control software. Most of them are beginner-friendly. There is plenty of GRBL support for beginners. Mach3 has a steeper learning curve in comparison.
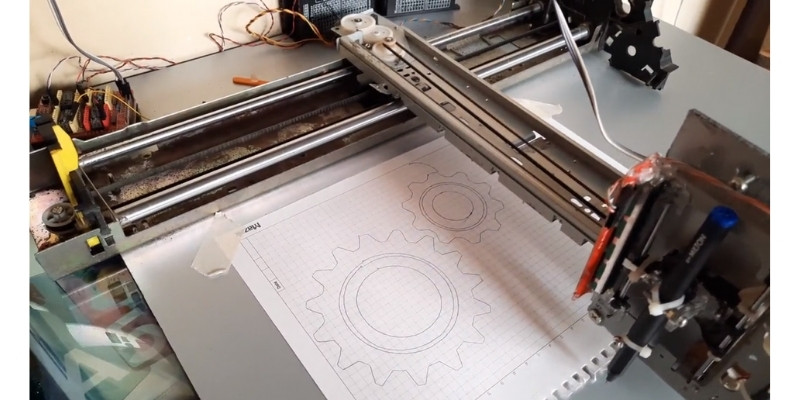
Moreover, the various GRBL control software generally have better UIs than Mach3. However, Mach4 has improved its UI greatly. Check out our article on Mach3 vs Mach4 for more differences between the two.
Also, OpenBuilds Control has a cool GRBL feature where you can jog your CNC with your cell phone.
Winner: GRBL is more user-friendly and beginner-friendly than Mach3.
Software | Ease of Use |
---|---|
Mach3 | Steep learning curve |
GRBL | User-friendly and beginner-friendly |
Capabilities
Mach3’s advantages over GRBL are in its capabilities:
- Mach3 (Mach4) can control a 6-axis machine (XYZABC) but GRBL can only control a 3-axis machine. The newer GRBL 1.1 can control 4 stepper motors.
- Mach3 supports Macro functions such as canned cycles. GRBL does not support these.
- Mach3 controls a CNC in almost real-time.
- Mach3 displays more relevant data to the user regarding machine position. However, this isn’t that important because you can always query GRBL if you want particular data.
But remember that these are not Mach3’s advantages over Arduino controllers. These are Mach3’s advantages over GRBL only.
To clarify, industrial controllers use microcontrollers as well, but they can be much more capable than Mach3 (Mach4). In fact, Mach3 used to be the cheap alternative to these controllers in the old days.
Plus, GRBL is not the only free controller firmware.
Additionally:
- G2Core (which is an Arduino controller) supports 9 types of axes and 6 stepper motors. So, Mach3 does not have any “axis advantage” over Arduinos – just over GRBL.
- You can use macro functions for GRBL with pre-processors such as G-Sharp which is open-source and free. So, Mach3 doesn’t have macro function advantages either.
- Regarding real-time control, you can already use feed hold and buffer wipe in G2Core (Arduino controller), so once again, Mach3 presents no real-time advantage over Arduinos – just over GRBL.
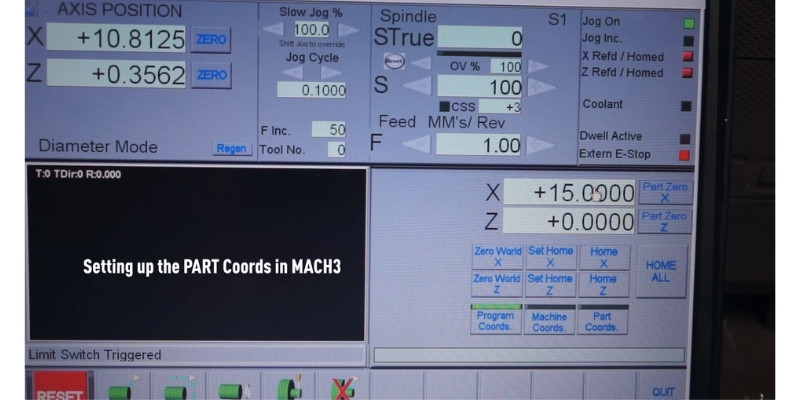
If you are using Mach3 only because GRBL does not give you 6-axis control, we have explained how to build a G2Core controller with Arduino Due in another article.
Still, G2Core is not fully developed, and since it’s free firmware, the development is slow at the moment.
Winner: Mach3 supports more features than GRBL
Software | Capabilities |
---|---|
Mach3 | Can control a 6-axis machine, Supports Macro functions, Controls a CNC in almost real-time Displays relevant data to the user regarding the machine’s position |
GRBL | Supports 3-axis machineMacro functions can be used with pre-processors such as G-Sharp which is open-source and freeAllows querying for particular data |
Bugs and Issues
LinuxCNC has fewer bugs and issues than Mach3. I don’t know whether Mach4 has taken care of all the bugs.
GRBL is very much alive and actively developed and has taken care of its major bugs. Still, they have not added a buffer wipe as far as I know. Also, I suspect that Mach3 may be more reliable than GRBL for long operations – but I can’t say that with certainty.
G2Core does not have persistent machine settings, so you have to save your machine settings in a file and paste them into the control software after each connection.
Winner: Tie. Mach3 is quite buggy, but Mach4 may be better for longer operations than GRBL
Software | Bugs and Issues |
---|---|
Mach3 | – Quite buggy |
GRBL | – Alive and actively developed, and major bugs have been addressed |
Room for Future Growth
This topic is important because if you spend a lot of time learning Mach3 and it gradually becomes outdated, you have wasted a lot of effort.
Generally, parallel porting with Mach3, Mach4, and LinuxCNC is getting outdated. Turning a computer into a CNC controller eliminated the need for a dedicated controller in the old days.
But Arduinos have since solved that problem. Parallel porting is an unnatural hardware setup in my opinion since it uses a computer’s motherboard instead of a dedicated microcontroller. Plus, computers have eliminated parallel ports, so they require USB BOBs.
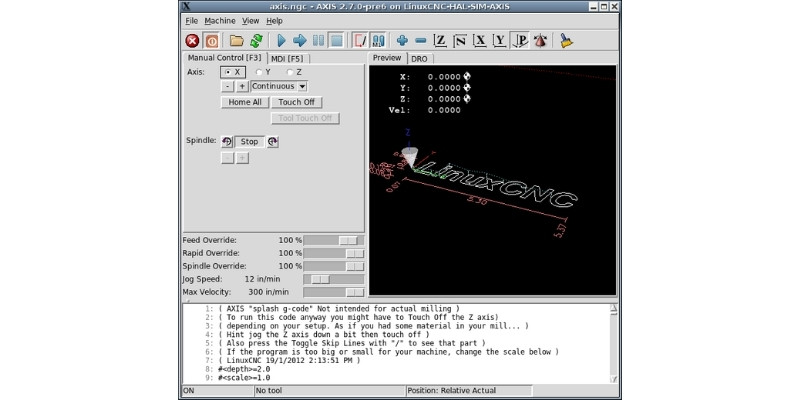
GRBL was only the first open-source Arduino controller, and it has already stolen the spotlight from Mach3.
Additionally, G2Core only occupies around 10% of its Arduino board’s memory and it already offers 6-axis control. Imagine what else the developers can do with the remaining 90% of the Arduino’s memory.
Winner: GRBL has a higher ceiling, with plenty of room left to grow
Software | Room for Future Growth |
---|---|
Mach3 | – Becoming outdated |
GRBL | – High ceiling, with plenty of room to grow |
Summary
Mach3 and GRBL use different hardware setups for a CNC controller. GRBL turns an Arduino board into a dedicated CNC controller. This hardware setup is the same as industrial controllers.
On the other hand, you can turn your computer into a CNC controller with Mach3 or LinuxCNC. This hardware setup requires breakout boards and optoisolators.
Function | GRBL | Mach3 |
---|---|---|
Price | ✅ | |
Control Software | ✅ | |
Ease of Use | ✅ | |
Capabilities | ✅ | |
Bugs and Issues | ✅ | ✅ |
Development Potential | ✅ |
So in short, for the question of GRBL vs Mach3
- GRBL is easier and more beginner-friendly than Mach 3. GRBL enjoys a variety of control software. It is free and open-source.
- On the other hand, Mach3 can control a 6-axis CNC, supports canned cycles, and controls a CNC in real-time. That said, other Arduino controllers are attaining all of these capabilities -which will make Mach3 and its unusual hardware setup outdated in the future.
Related Posts:
- How to Connect Stepper Motors to Arduino/GRBL With and Without a CNC Shield
- Wiring Stepper Motors (With 4, 5, 6, and 8 Wires): Unipolar, Bipolar Series, Bipolar Parallel, and Bipolar Half Coil
- The Best DIY Laser Cutters & Engraver Kits
- Best Entry Level CNC Plasma Tables
- CNC Shield Guide: Can You Use Arduino and GRBL with Powerful CNCs
- The top GRBL software options for controllers