Key Takeaways
- Arduino CNC basics: Arduino is a microcontroller that can run GRBL firmware to control CNC machines.
- Arduino CNC shield: A board that connects Arduino to stepper motors, spindles, and other parts. Optional for some drivers.
- Arduino CNC limitations: Arduino can only handle low-current stepper motors and weak spindles. Not suitable for large CNCs.
- Arduino CNC alternatives: Other controllers that can handle more powerful motors and spindles. Examples: Mach3, LinuxCNC, TinyG.
Assembling a DIY CNC involves putting together its controller. You have three options when choosing a CNC controller – you can:
- Buy an industrial controller
- Turn your computer into a CNC controller
- Turn an Arduino board into a CNC controller
If you want to know how to turn an Arduino board into a controller like GRBL, read our previous article.
Using an Arduino CNC shield is the most popular way of connecting a CNC controller because the CNC shield sits on the Arduino and connects to parts that an Arduino can’t.
However, this method’s convenience has led to a common misunderstanding online: that CNC shields are the essential electronics for using Arduino controllers.
Therefore, in this article we explain whether a CNC shield is electronically necessary, and if so, to what extent you can use a CNC shield. We also explain CNC shield alternatives, and whether you can mix CNC shields with other methods.
Do You Have To Use a CNC Shield?
A CNC shield is only electronically necessary with certain types of stepper motor drivers. CNC shields are usually insufficient in driving spindles, but they’re still useful if not necessary, as they can give you more limit switch pins, emergency stop pins, coolant switching, and more.
We also have an article covering the best CNC shields, to help you pick the best shield for your Arduino controller.
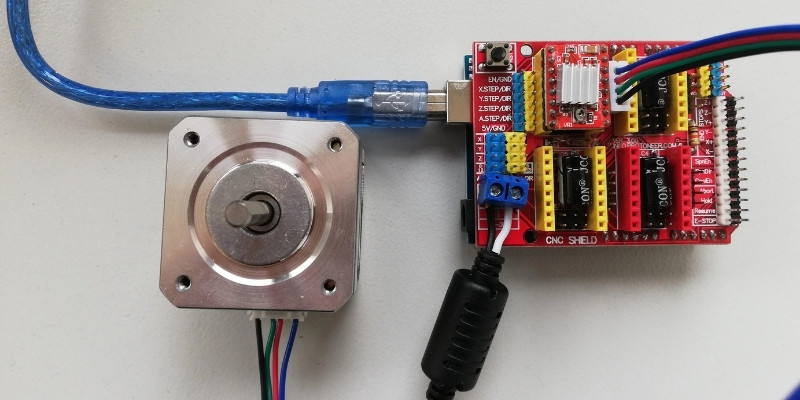
What is an Arduino CNC Shield?
An Arduino CNC shield is an electronic board that you can attach directly to an Arduino board. It sits between the Arduino and stepper motors.
An Arduino controller can’t directly move a stepper motor. It needs stepper motor drivers.
The CNC shield has these stepper motor drivers and output pins that connect to the stepper motors and other parts like the spindle or the coolant.
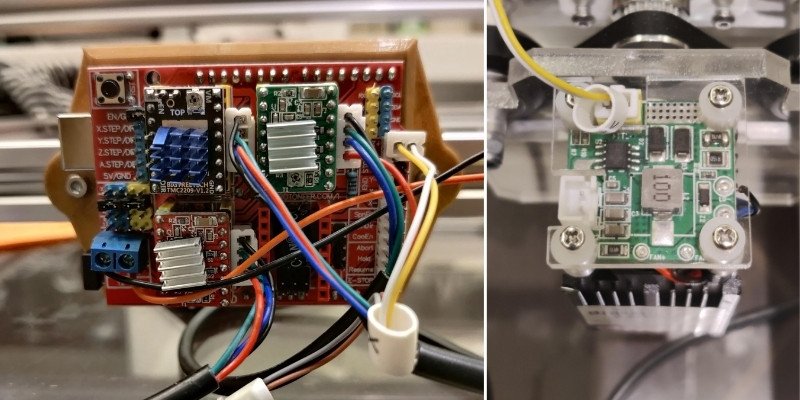
What Does a CNC Shield Do?
A CNC shield serves the following purposes:
- A CNC shield has electronics for stepper motor drivers. (Also, a CNC shield might have stepper motor microstepping.)
- Electronics to turn on a spindle or a laser. Plus, a CNC shield should have pins for spindle speed control (PWM).
- A CNC shield has pins for limit switches and end-stops. Also, it can have pins for probing.
- Some CNC shields can turn on the coolant (if your CNC has a coolant).
Next, we will explain what a CNC shield brings to the table regarding these tasks.
In short, whether a CNC shield is necessary for stepper motors depends on your stepper motor driver.
Meanwhile, CNC shields’ electronics for spindles are too weak, so you will need other means to drive spindles.
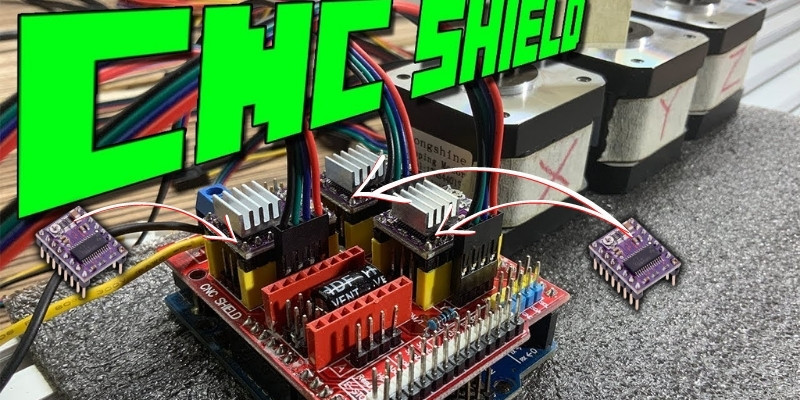
Is an Arduino CNC Shield Necessary for Stepper Motors?
The short answer is it depends on your stepper motor driver. If you use stepstick drivers like DRV8825 or A4988, it is best to use a CNC shield.
But if you use stepper motor drivers like TB6600 or DM542T, you don’t need a CNC shield.
What Is the Difference Between The Two Types of Stepper Motor Drivers? Stepstick Drivers vs Stepper Motor Drivers
Stepstick drivers are small electronic stepper motor drivers.
They need at least one capacitor to work, but they also need other electronics to improve their performance.
A CNC shield provides this circuitry for stepper motor drivers.
However, stepper motor drivers (like the TB6600) already have the necessary electronic circuitry inside. They also have filters to resist noise, and so don’t require a CNC shield.
Some CNC shields can do microstepping while others can’t. The CNC shields that have microstepping, usually provide up to 1/8, 1/16, or 1/32 microstepping with the stepstick drivers.
On the other hand, external drivers (like TB6600) have microstepping (up to 1/32) on them with jumpers.
Stepstick drivers are appropriate for low-current stepper motors (usually below 1.5 amperes per phase). But stepper motor drivers like TB6600 are suitable for higher-current stepper motors.
In short, CNC shields take care of the necessary circuitry for stepstick drivers, but they don’t bring any crucial functions to standalone stepper motor drivers.
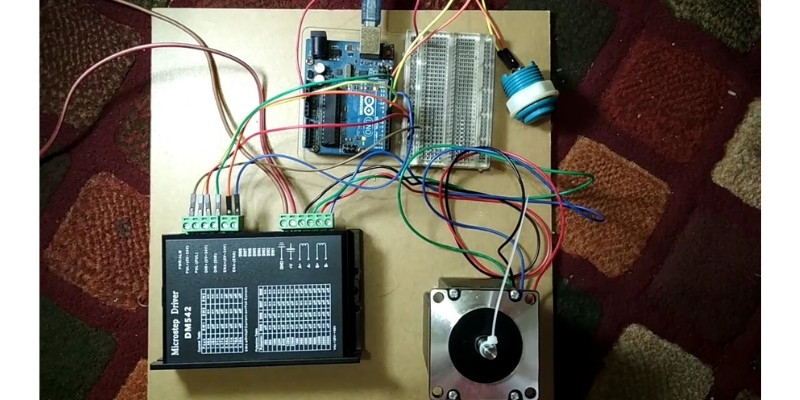
Pros and Cons of CNC Shields With StepStick Drivers
A CNC shield with stepstick drivers offers the following:
- A CNC shield eliminates the wiring from the Arduino to the stepper motor drivers.
- A CNC shield sits on top of the Arduino and takes up a small space. Plus, it looks immaculate since there are no wires between the controller and the shield.
- Most CNC shields can power up the Arduino directly from the power supply.
However, some cons of CNC shields include:
- CNC shield stepper motor drivers are weak. They are only appropriate for low-current stepper motors. So, they are a solution for lasers, 3D printers, and small CNCs.
- CNC shields generally have poor heat dissipation. This is due to packing several stepper motor drivers in a small space. This increases the possibility of burning your stepper motor drivers.
- Replacing a burnt stepper motor driver is difficult (and sometimes impossible) if the shield comes with soldered drivers.
On the other hand, standalone stepper motor drivers are appropriate for midsize or large CNCs, 5-axis CNCs, and CNC mills.
These stepper motor drivers produce better outputs for stepper motors (they have better filters and generate smoother and better waves).
Plus, external drivers usually contain short-circuit detection and prevention circuits. Some CNC shields include these functions as well.
How to Decide Whether a CNC Shield Is Necessary for Your Stepper Motors?
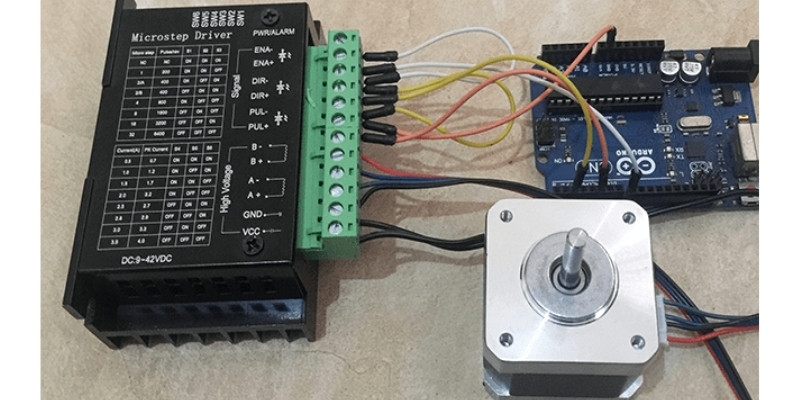
Use a CNC shield if your machine is a laser, 3D printer, PCB printer, or a small CNC router. These machines require small and weak stepper motors.
If you are unsure about your midsize CNC, follow these steps.
- Firstly, you should decide on your stepper motors. As a rule of thumb, small CNC routers require smaller and weaker stepper motors, while bigger CNCs with more powerful spindles need more powerful stepper motors. Check out our article on the best stepper motors for CNC for more.
- Choose the appropriate stepper motor driver based on its current per phase. You can often ignore your stepper motor’s voltage rating and focus on its current rating to choose its stepper motor driver. (We’re not discussing huge stepper motors with unusual voltages here.)
- Now you’ve decided either on a stepstick driver, or a stepper motor driver with a complete electronic board like TB6600. This answers whether a CNC shield is necessary.
Can CNC Shields Drive Spindles?
Yes, most CNC shields have pins to drive spindles. This includes turning a spindle on or off, and controlling its speed.
First of all, most small CNC routers or hobby-level CNC routers use routers – not spindles. For example, the X-Carve uses a Dewalt router, while the Shapeoko usually employs a Makita router.
Read more: X-Carve vs Shapeoko CNCs compared
Still, Shapeoko gives you the option of using a 65mm spindle. We have explained in another article how you can achieve accurate speed control with spindles but not routers.
So the CNC shield does not do much for a CNC router that uses a router.
But if you have a spindle, there is a lot you should know about the limitations of CNC shields in working with spindles.
CNC Shield’s Spindle Enable Pin
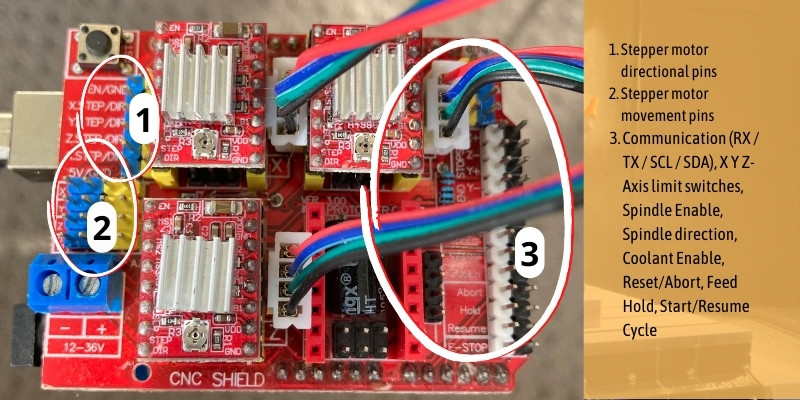
Almost all Arduino CNC shields can only switch extremely weak spindles on or off. We’re talking about 24v and 240W spindles or, in some cases, 48v and 480W spindles.
So, you still need external electronics to switch most spindles.
CNC Shield’s PWM Pin
Regarding spindle speed control, CNC shields have a PWM pin that can control a spindle’s speed.
But, the Arduino already has a PWM pin. So, the question is whether the CNC shield’s PWM is better than the Arduino’s.
The Arduino’s PWM pin can only control a small spindle speed range (usually up to 10000 RPM).
Many CNC shields out there can achieve the same speeds, and their PWM pin directly connects to the Arduino.
However, some CNC shields offer improved speed control. They take the PWM from the Arduino and boost it to handle speeds up to 20000 RPM.
So, while some CNC shields are worthless in spindle speed controls, others are useful. Nevertheless, you can also control spindle speed without CNC shields.
In short, CNC shields are usually insufficient for driving spindles.
Can You Still Use a CNC Shield If It Is Not Necessary?
If you have decided you need external stepper motor drivers, you can still use a CNC shield with external drivers.
CNC shields have several pins beside their stepper motor drivers for use with external drivers. Although you will have to use DIY wiring for your stepper motors this way, using a CNC shield can provide you with some benefits.
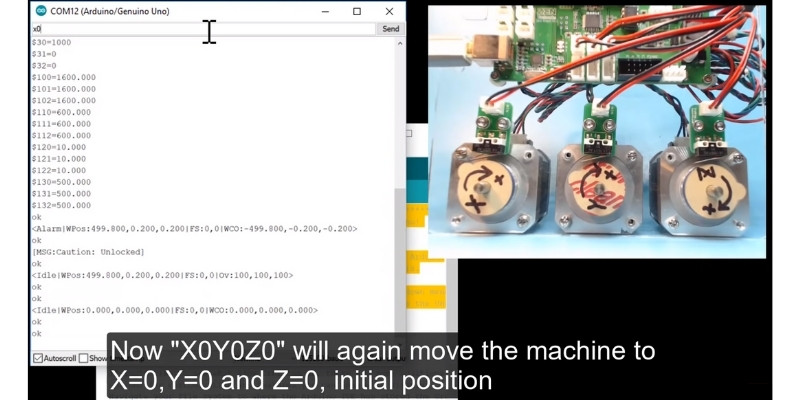
For example, Arduino Uno has one 5v pin, so you must wire all the stepper motor drivers to it. But a CNC shield gives you several 5v pins to use (usually 3 or 4 pins).
Or you can use the CNC shield’s limit switch pins. Once again, the Arduino has the limit switch pins, so the CNC shield is unnecessary.
But GRBL provides three limit-switch pins while you often get six limit-switch pins with a CNC shield. So it is more convenient to use a CNC shield with GRBL.
If your CNC has a coolant system, there are many CNC shields that can switch your coolant. So a CNC shield can eliminate the need to wire the coolant to necessary electronics.
You can also use the CNC shield’s pins for the spindle, although we have discussed the limits of CNC shields with spindles.
Plus, you can power your Arduino from a CNC shield.
But you can’t use the CNC shield’s stepper motor output pins with powerful stepper motors. You should connect your stepper motors to the external stepper motor driver per the DIY wiring method.
Summary
Arduino controllers (like GRBL) need supplementary electronics to connect to other parts like stepper motors.
A CNC shield has the necessary electronics for 3D printers, lasers, and small CNC routers. But a CNC shield is unnecessary if you use external stepper motor drivers.
Still, you can use a CNC shield alongside external drivers if you want to upgrade your stepper motors.
Using a CNC shield allows you to exploit other benefits of CNC shields, like more limit-switches and switching a coolant.
Finally, CNC shields have many limitations in driving a spindle.
Related Posts:
- How to Connect Stepper Motors to Arduino/GRBL With and Without a CNC Shield
- How to Build a GRBL or G2Core Controller for CNC, 3D Printer, or Laser
- CNC Programming: A Complete Beginner’s Intro (Guide)
- Best GRBL Controller Software