Key Takeaways
- CNC routers vs mills: The article compares the differences between CNC routers and CNC mills, two types of machines that can cut complex shapes from materials.
- Structure and movement: CNC routers have a gantry design where the spindle moves on the X, Y, and Z axes, while the workpiece remains stationary. CNC mills have a table that moves on the XY plane, while the spindle moves on the Z-axis.
- Material compatibility: CNC routers are better for softer materials like wood and plastic, while CNC mills are better for harder materials like steel and titanium.
- Other differences: The article also covers other aspects that differentiate CNC routers and mills, such as work area, Z clearance, tooling, rigidity, accuracy, spindle speed, feed rate, and coolant systems.
The main differences between CNC mills and CNC routers are that CNC mills are better for hard materials like steel, have a larger Z-axis movement and are great for tall material blocks, and are more rigid and accurate since they move the table, not the workpiece.
Though, CNC routers have larger work areas and are better for sheet materials.
Other differences include CNC mills employing a lower spindle speed, and CNC routers being able to use a straight router bit, while CNC milling machines always use spiral end mills.
I personally use my CNC router to cut and engrave sheets of wood, PVC, MDF, and even engrave sheets of stone. I use a CNC milling machine for any harder materials.
As examples, I’ll use two machines costing around $10,000 to show the differences: the X-Carve Pro (CNC router) vs Tormach PCNC 440 (CNC mill).
Feature | CNC Router | CNC Mill |
---|---|---|
Structure and Axis Movement | Workpiece is stationary, spindle moves on X, Y, and Z axes | Workpiece and spindle both move, spindle moves on Z axis |
Material Compatibility | Better for soft materials like wood, and soft metals like aluminum | Better for hard materials like steel, cast iron, and titanium |
Work Area | Larger work areas, suitable for large sheets of soft materials | Smaller work areas, suitable for smaller hard material blocks |
Z Axis and Material Height | Z-clearance is limited due to gantry design | Greater Z-clearance due to independent Z-axis |
Tooling | Can use a wider range of cutting tools, including straight router bits | Typically uses spiral end mills |
Rigidity | Less rigid due to gantry design | More rigid due to independent C-frame |
Accuracy | Lower accuracy due to less rigidity | Higher accuracy due to better rigidity |
Spindle Speed | Higher spindle speeds, useful for cutting soft materials | Lower spindle speeds, useful for cutting hard materials |
Feed Rate (Speed) | Faster feed rates due to higher RPMs | Slower feed rates due to lower RPMs |
Coolant Systems | Typically doesn’t have coolant systems | Includes coolant systems to manage heat from hard material machining |
Table of Contents
Similarities Between CNC milling machines and CNC Routers
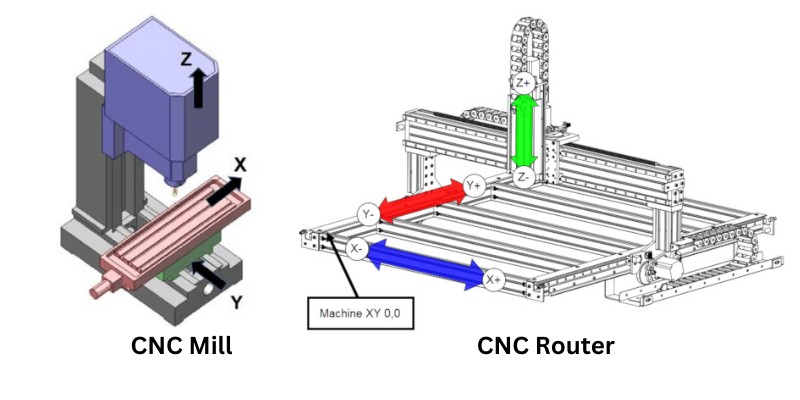
Let’s start with the similarities.
Both CNC routers and CNC milling machines do subtractive manufacturing, unlike 3D printers that perform additive manufacturing. Subtractive manufacturing means they cut material blocks down, remove material, and cut complex shapes and parts out of the workpiece.
Both types of CNC machines also use CAD and CAM software to generate the G-code (the language CNC machines use to cut).
Both CNC routers and mills also have similar axes: the Y-axis is the longest and moves front to back, and the X-axis moves left to right.
Now, the differences.
CNC Mill vs Router: All the Differences
Structure and Axis Movement
One of the key differences between routers and CNC mills is their different structures and axis movements. CNC routers typically use a gantry, while CNC milling machines typically have a moving table and a C frame.
CNC routers typically use a gantry design where the workpiece remains stationary on the table. The gantry, which moves on the X and Y axes, carries the CNC router spindle to cut the material.
This spindle moves along the Z-axis (up and down), which is mounted on the gantry that moves along the X-axis (left and right). The entire gantry assembly can then move along the Y-axis (forward and backward).
The image below shows X-Carve Pro and how it moves:
This gantry design is the same way that other CNC machines work, like 3D printers, PCB printers, and CNC plasma tables.
On the other hand, CNC mills typically have a table bed that holds the workpiece, which moves along the XY plane (more advanced machines can also move along the Z plane).
The CNC mill’s spindle then typically moves up and down the Z plane, positioned on a C-frame that moves independently to the XY table.
You can see this in the image below:
So, CNC mills also differ to CNC routers as both the workpiece and spindle can move, whereas with gantry designs on CNC routers only the spindle moves.
These are just how the common 3-axis CNC mills and routers work however. Some other CNC machinery, like modern CNC lathes, are often equipped with “live tooling” or “C-axis” capabilities, which mill materials, providing another level of versatility. Though, this article solely focuses on CNC mills vs routers.
Material Compatibility
CNC mills are better for working on hard materials, like steel, cast iron, and titanium. This is because of their better rigidity, more powerful and lower-speed spindles, better precision, and they often use more durable tooling and more effective coolant systems.
However, CNC routers are generally better for soft materials like wood, and soft metals like aluminum and brass.
This is because they cut faster with high spindle speeds, can cut larger wood and aluminum sheets with their larger working areas, and they often have effective dust collection systems when cutting wood.
Generally, CNC routers can cut up to about an inch in one pass. We published a guide where we explain how deep can a CNC router cut, the factors that affect cutting depth, and more.
Our example machines show this material difference. The X-Carve Pro can process wood, acrylic, and nonferrous metals like aluminum, brass, and copper. But, our example CNC milling machine, the Tormach PCNC 440, can even cut steel.
Material | CNC Router | CNC Mill |
---|---|---|
Wood (sheet) | ✅ | ❌ |
MDF (sheet) | ✅ | ❌ |
Plastic (sheet) | ✅ | ❌ |
Foam | ✅ | ❌ |
Aluminum 6061 | ✓ (if the part is not tall) | ✅ |
Gold | ✓ | ✅ |
Silver | ✓ | ✅ |
Brass | ✓ | ✅ |
Bronze | ✓ | ✅ |
Copper | ✓ | ✅ |
Platinum | ❌ | ✅ |
Aluminum 7075 | ❌ | ✅ |
Iron | ❌ | ✅ |
Steel | ❌ | ✅ |
Cast Iron | ❌ | ✅ |
HSS (High-Speed Steel) | ❌ | ✅ |
Titanium | ❌ | ✅ |
Work Area
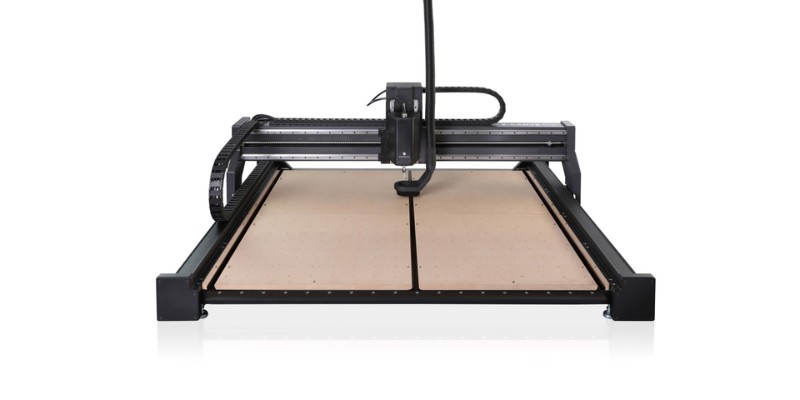
CNC routers generally have larger working areas than CNC mills. This makes them more suitable for cutting large material sheets of softer materials.
For example, the working area of the X-Carve Pro CNC router is far larger than the Tomach PCNC 440 mill:
X-Carve Pro (Router) | Tormach PCNC 440 Mill | |
---|---|---|
Work Area | 48”×48” / 1220mm×1220mm | 10”×6.25” / 254mm×159mm |
Z Axis and the Material Height
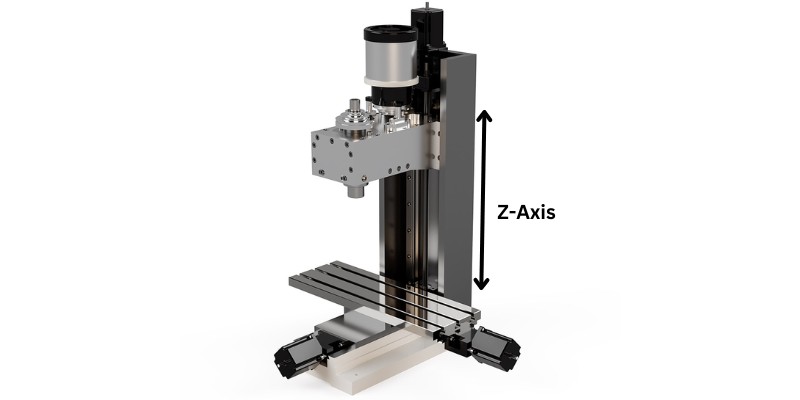
CNC mills can have higher Z-clearance than CNC routers, but this largely depends on the specific model and design. It’s common to find CNC routers with between 2 to 15 inches of Z-axis movement, while some CNC mills can offer up to 3 feet. However, these values can vary significantly across different models and manufacturers.
The structural arrangement of the Z-axis contributes to these differences.
In a CNC router, the Z-axis is typically mounted on the gantry, limiting the available room underneath it. Most entry-level CNC routers have just 2” of Z-clearance, though the DIY CNC router I personally built for myself had 6” clearance.
In contrast, CNC mills usually feature an independent Z-axis mounted on a column, which can allow for greater Z-clearance, though it depends on the specific machine.
For example, the X-Carve Pro CNC router provides 4″ of Z-clearance with risers, while the Tormach PCNC 440 CNC mill offers 10″.
So, while CNC machining tall materials is possible with a mill, the gantry systems CNC routers have creates serious limitations in the material height they can carve.
Tooling
CNC milling machines typically use spiral end mills, while CNC routers can use a much wider range of cutting tools, especially when working with softer materials like wood.
This is because CNC cutting tools fall into two categories: straight router bits, and spiral end mills. Straight router bits have straight sharp edges, while spiral end mills have helical cutting edges to help with chip evacuation.
I personally use straight router bits to cut softer materials like wood, due to the excellent finish they provide. However, straight router bits should not be used on metals, as it generates excessive heat, poor chip evacuation, and damage to your cutting tool.
Spiral end mills, used by CNC mills, are the better choice for cutting metals. They’re designed to handle the heats and load that occur when cutting harder materials.
So, while spiral end mills are commonly used in CNC milling machines, the tool you need mostly depends on which material you’re cutting. But generally, CNC routers have access to a more versatile range of tooling options.
Rigidity
CNC mills are generally far more rigid than CNC routers, as they are typically built using more robust materials, and the design allows for better rigidity.
In a CNC router, the gantry is supported mainly by the linear movement mechanism, which has to handle both the load of the spindle and the forces of cutting.
But in a CNC mill, the table moving mechanisms only have to support the weight of the table and workpiece, while the C-frame independently supports the Z-axis. This design makes for better rigidity.
Furthermore, the design of CNC routers can make them susceptible to bending. For example, when the spindle is moved towards the ends of its working area, this gets away from the center of mass from the gantry, creating a large rotating torque that also affects precision.
While I personally have succeeded in building a very rigid CNC router, this took a lot of time improving the design to be more rigid, since the gantry is not inherently strong.
Accuracy
CNC mills are generally more accurate than CNC routers, as the accuracy of a CNC machine heavily depends on its rigidity, among other factors.
CNC mills can reach accuracies of 0.01mm with the right CNC mill, quality tooling, and optimal operating conditions. This accuracy is why a CNC mill is ideal for machining hard metals.
This level of precision makes CNC mills a preferred choice for machining hard metals, especially in industries such as automotive, aerospace, and marine, where high-precision parts are essential.
Many industries do prefer using routers for some projects. We list those industries in What industries are CNC routers used in?
Many CNC routers claim a 0.01mm accuracy as well, but this depends on the material and the CNC router’s rigidity. CNC routers So, CNC routing wood, which requires lower precision capabilities, is generally more appropriate.
While many CNC routers also claim a 0.01mm accuracy, this depends on the router’s rigidity, the type and condition of the cutting tool, and the material being machined. Given these considerations, CNC routers are generally best suited for materials like wood, where there are lower precision requirements.
Spindle Speed
CNC routers typically operate at higher spindle speeds than CNC mills.
CNC mills, which often work with hard metals, need to provide high torque at lower speeds. CNC routers, which are often used for softer materials like wood and aluminum, employ high-speed spindles that allow for faster cutting.
In general, you can expect a CNC mill spindle to have a maximum speed of around 10,000 RPM, while a CNC router’s spindle may operate at speeds of 24,000 to 30,000 RPM.
For example, X-Carve Pro’s spindle can run at 24,000 RPM, while the Tormach PCNC 440’s spindle runs under 10,000 RPM.
I have personally cut wood with a CNC router at 20,000 RPM, whereas I’ve used 500-1500 RPM when I’ve cut metal with a CNC mill.
It’s also worth noting that some beginner CNC routers use a traditional handheld router as a cutting tool instead of a spindle (a router is a cheap alternative to a spindle, not to be confused with the CNC router). These routers are not used in CNC mills, which require greater precision. We also have a more in-depth article on CNCSourced covering the differences between a router and a spindle.
Speed (Feed Rate)
CNC routers often operate at faster feed rates and spindle speeds than CNC mills. The main reasons for this include:
- Higher RPMs: CNC routers typically work with softer materials like wood, which can be cut at higher rotational speeds, leading to higher RPMs.
- Higher Feed Rates: To maintain a high chip load, CNC routers typically operate at higher feed rates than CNC mills.
For instance, when I cut wood on my CNC router, my machine moves at around 2000mm/s, and I sometimes have to lower the RPM because my CNC machine’s speed is still too low.
In terms of specific examples, the X-Carve Pro has a maximum feed rate of 300 IPM (inches per minute), while the Tormach PCNC 440 Mill maxes out at 135 IPM.
So, although particular mills may be faster than particular routers, CNC routers are generally faster.
Coolant Systems
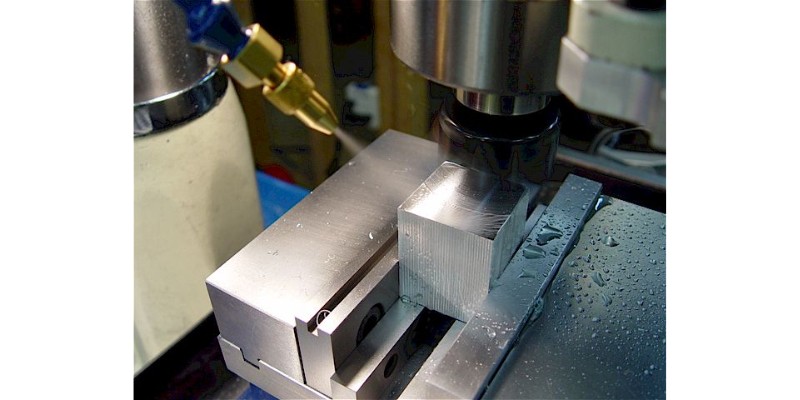
CNC mills generally include cooling systems due to the significant heat generated when machining hard materials such as metals. CNC routers do not typically have coolant systems.
This cooling system typically sprays a coolant on the milling cutters and the workpiece to maintain the right temperatures and prevent damage to the tooling.
Because CNC routers usually cut softer materials like wood and plastic, they don’t need coolant systems, as they do not generate enough heat generated when cut to require cooling.
However, there can be exceptions. For example, when I used my CNC router to engrave stone — a significantly harder material — I created a cooling system that maintained a steady flow of water into the cutting area to help manage the heat.
FAQs
Is a CNC router the same as a CNC mill?
No. CNC routers and mills have different axis movements, look completely diferent, have different working areas, different materials they’re better suited for, and differing speeds, rigidity, accuracy, and more.
What is the difference between a router and a mill?
With CNC routers, the workpiece lays still as the gantry moves around, whereas in CNC mills the workpiece moves in the XY plane.
Therefore, CNC routers can work on large sheets of soft material like wood and plastic, while CNC mills can work on very hard materials like steel and titanium that are smaller in size.
The main difference between CNC routers and CNC mills lies in the way they move relative to the workpiece. In a CNC router, the workpiece lays still on the machine bed while the gantry moves, while CNC mills feature a moveable bed that moves across the X and Y axes, while the spindle moves down the Z-axis.
Can I mill with a router?
Yes, it’s possible as long as the workpiece isn’t too tough and isn’t too tall, but your results will be limited versus just using a CNC mill. This is because CNC routers lack the same rigidity, spindle power, and have a lower torque gantry design that isn’t well suited to milling metal.
Check out our other CNC mill and router articles:
- The best metal CNC machines for aluminum
- The best CNC mills 2022
- The 11 best DIY CNC routers 2022
- Best cheap CNC routers in 2022
- Making money with your CNC router
- How much does a CNC cost? CNC machine Price guide