Key Takeaways
- Stone hardness: Choose a bit that is harder than the stone. Diamond or tungsten carbide bits are best.
- Cooling system: Use water to cool down the engraving area and prevent overheating and cracking.
- Machine rigidity: Your CNC machine should be strong and stable enough to handle the force and resistance of stone.
- Feeds and speeds: Adjust your feed rate and spindle speed based on your stone type, bit size, and machine power.
There is something about engraving on a stone that is beautiful and addictive. Stone is a symbol of strength and hardness, and engravings stay for hundreds of years.
But can you engrave on stones, or even granite, with a CNC machine?
Do you have to buy a granite CNC machine (which costs between $6000 to $40000), or can you modify your CNC machine to cut stones including granite?
Stone engraving has many purposes – some big and some small. On the larger side, stone industries use huge CNC machines to cut and chamfer stones for countertops and buildings.
Meanwhile, some are in the business of engraving headstones. At $20-25 per character, engraving headstones costs between $500 to $1500.
On the smaller side, some engrave decorative stones with personalized messages for use around the house and especially in gardens.
Can you do any of that with a CNC router? The answer is yes.
In fact, I turned my machine into a granite engraving CNC machine with just a $5 bit, so here are my tips and tricks for CNC engraving stone.
This guide explains how the scratch hardness of your stone, the hardness of your bit, your CNC machine’s rigidity for granite and stone, spindle power, and the correct feed rate and speed affect carving.
Plus, I’ll show you how to make an automatic cooling system for stone engraving.
CNCSourced is reader-supported. When you buy through links on our site, we may earn an affiliate commission. Learn more
Sandblasting vs CNC Machining Stones
When it comes to engraving large stones, sandblasting is the cheaper and easier option for several reasons:
- With sandblasting, you don’t need to worry about whether the stone is perfectly flat for V-carving.
- It takes more effort to set up the stone in a CNC machine.
- It is generally easier to sandblast since you don’t need to calculate feeds and speeds and find the right bit and the right CAM tool path.
For these reasons, CNC is not very popular with stones. Still, CNC machining stone has some advantages over sandblasting as well.
- CNC machines have many more applications besides engraving. There are huge industrial stone-cutting CNC machines that cut stones with custom shapes for buildings.
- CNC produces a smoother finish. With CNC, you still don’t get a perfectly smooth surface due to stepover, but the remaining lines are very fine and orderly. For example, you can emboss a text with fine finishing and an orderly horizontal line pattern on the pocketed area.
- Sandblast can’t cut stones. CNCs can cut stones as well as chamfer or create various patterns on stones.
Laser Engravers vs CNC Stone Engravers for Granite and Marble
A laser engraver is an impressive option for engraving on granite with great detail, but can’t carve stone.
CNC is also better suited for marking stone generally because
- CNC stone carvings look better. You can touch and feel the carving, and see the contrast.
- Plus, an engraved stone remains for hundreds of years while laser engravings only survive on granite for around 50 years.
As a result, laser engravers are better for very fine detail engravings such as engraving a picture while CNC engraving is better for larger uses like text engraving.
Can CNC Machines Engrave and Cut on Granite and Marble?
Yes, if the CNC machine is rigid and powerful enough, you can cut granite with the right bit. Also, engraving is easier than cutting.
Midsize rigid CNCs can engrave on granite. But for cutting and chamfering large stones, you need large, expensive CNC machines with special bits.
From Marble to Granite: Know Your Stone’s Hardness
One of the most important parts of engraving a stone is knowing your stone’s hardness – and your bit’s hardness.
When you rub two stones on each other, the tougher one scratches the softer one. Similarly, if the stone is tougher than your router bit, it will scratch and destroy your bit.
So, how do we know the hardness of the stone?
Scratch hardness shows how resistant a material is against scratching or engraving with a sharp object. We are only interested in scratch hardness, not rebound or indentation hardness.
We use the Mohs scale for calculating scratch hardness – measured from 1 to 10.
For example, you can scratch gold (Mohs scale of 2.3 to 3) with iron (4.5). But you can’t scratch iron with gold.
This becomes important for CNC machinists because it allows them to choose a bit that can scratch their material.
Here is the Mohs scale of some interesting metals:
Material | Scratch Hardness |
---|---|
Zinc | 2.5-3 |
Gold | 2.5-3 |
Aluminum | 2.5-3 |
Steel | 4-4.5 |
Iron | 4.5 |
Here is the Mohs scale of some interesting types of stone:
Stone | Scratch Hardness |
---|---|
Limestone | 2-3 |
Marble | 3 |
Travertine | 3 |
Granite | 6-7 |
Nano stone | 6-7 |
It is far easier to engrave on marble than on granite since granite is very hard to scratch.
Use the wrong bit, and you’ll destroy it almost instantly as it comes into contact with granite, as if your bit is in a lathe and the stone is the cutter.
Which CNC Bits Can Engrave Granite and Stone?
There are many bits that advertise stone engraving. But a lot of them don’t tell you what stone they can cut. Most of these bits can cut marble, but fail miserably at scratching granite. Why?
To cut stone, you need either a carbide or diamond bit.
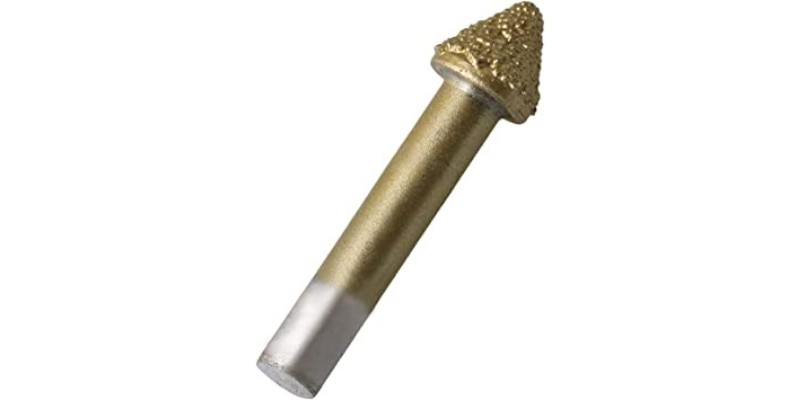
Carbide is a very tough material. Some carbide tools can engrave on granite. And many stone engraving bits are made from carbide or at least have a carbide coating.
However, there are various types of carbides, such as iron carbide, chromium carbide, chromium-vanadium carbide, and more. Each has different levels of hardness.
If you want to engrave on tough stones such as granite, you need a diamond bit or a tungsten-carbide bit. Other carbide bits can’t engrave granite.
PCD (Polycrystalline Diamond) is an artificial diamond. It has a Mohs scale of 10. Diamond is the toughest material you can find and can cut even the toughest materials.
Tungsten carbide is also very tough. Its Mohs scale is 8.5-9. Bits that are closer to 9 on the Mohs scale are also very tough and can engrave granite.
Best CNC Bits for Stone and Granite Engraving
Some PCD bits are very expensive. I have seen some V-bits go from $200 to $2000. This is because of how difficult it is to craft a perfect V bit out of PCD – after all, to create one, what do you cut it with?
Some of the diamond bits I see are carbide end mills that have particles of PCD scattered on their surface like a powder. To make such a PCD bit, the manufacturer doesn’t have to cut the diamonds. These bits are cheaper, but they can’t engrave, just cut.
However, there are some cheap PCD bits that come from China. Only the tips of these bits are diamonds.
For example, here is one on Alibaba that costs less than $5.
They even show a video clip in which the bit is engraving a stone that looks like granite. They have short bits from 60° to 150° with thick steel bodies that prevent tool deflection. So, these are the best bits for granite engraving
This is a similar item on Amazon which is again, from China. They are reselling it for under $15.
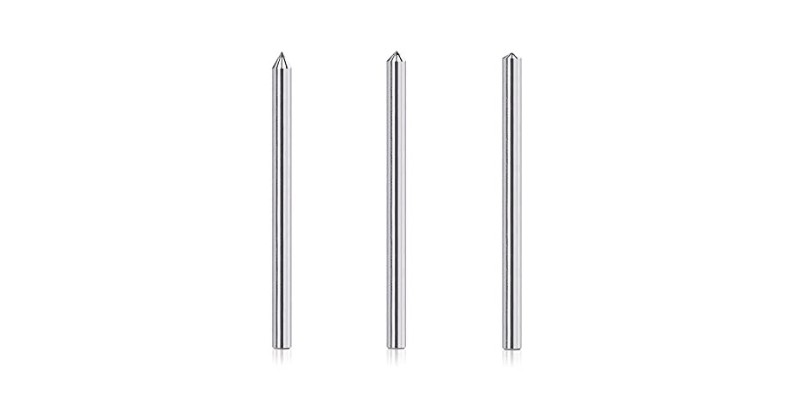
Because only the tips of these bits are made from diamonds, you should never plunge your tool deeper than the diamond tip (the depth of cut is around 1.5mm with these tools).
If you need a cheap bit for deeper engraving (of larger texts) consider the tungsten carbide bit we introduce next.
A $5 Tungsten Carbide Bit for Stone Engraving
Alpen is an Austrian drill bit manufacturer. They do not make router bits for CNC, they make drillbits, but some of their special bits have a V-shaped end that tempts us to try V-carving with them.
So, a few years ago, I used their multipurpose red drill bit as a CNC V bit and it produced good results. This is the only tungsten carbide bit I know of that can engrave on granite. You can see a picture of this bit below.
On top of that, they have another blue bit specifically for granite, marble, and stones that has the same shape and geometry. I haven’t tested that one, but it should work out well too.
The Alpen multipurpose drill bit is made out of tungsten carbide with a real hardness of 9 on the Mohs scale. It cost me less than $5, and if I remember correctly, I calculated its V angle to be 130°.
Alpen multipurpose drill bits come in different widths and lengths.
The ones I see on Amazon are too long and not appropriate for engraving. If you want to use it as a router bit in your CNC, you should get the shortest one you can. Also, you should get one with at least a ¼ inch shank, as this reduces tool deflection.
You can see in the picture below the original bit on the left. I have custom-cut the one on the right to avoid tool deflection.
The width is up to you. For finer and smaller engravings, you may choose smaller bits. But note that larger bits can do the same engravings but they need shallower plunges.
So, I suggest that if you want to engrave on hard stones like granite, go with larger bits that require shallower plunges and have larger shanks.
I have used Alpen multipurpose drill bits on Travertine with large plunges in the 3mm range and it had no problem cutting. It could even cut the sheet in several passes.
Granite & Stone CNC Machines Must Have a Cooling System
Engraving on stone generates tremendous heat, so granite-cutting CNC machines must have a cooling system.
If your CNC machine does not have a cooling system, you can build one for stone engraving.
It can be as simple as attaching a hose that runs water on your engraving area. But I made a more sophisticated cooling system a few years ago when I wanted to test stone engraving.
I made a tub of water out of PVC that lay filled under the engraving area. It would also collect the water that fell from the sides of the stone.
I had a pump in the corner of the tub that would thrust water into a hose that came all the way to the bit.
Chips and particles of stone would also accumulate on the tub’s bed, so it is better to have the pump in a corner away from these particles. Still, these particles are heavy and will not move toward your pump.
You can turn on the cooling system before you start engraving, or have an electronic system that turns it on automatically.
For turning the pump on automatically, I connected the “spindle on” pin of my CNC machine’s controller to a relay that would turn on the pump automatically.
What Kind of CNC Machine Can Cut Granite, Marble, and Other Stones?
If you want to cut or engrave stone with your CNC, it needs to meet some requirements.
The requirements for engraving are lower than for stone cutting. You already know that a cooling system is essential.
Here are some other requirements.
CNC Rigidity for Stone Cutting
Cutting stone requires exerting much more force than cutting wood, for example. So, you need a CNC machine that is rigid. If your CNC machine is not rigid enough for stone, it will be inaccurate.
Once again, cutting requires more rigidity than engraving.
What Spindle Power Do You Need to Cut Stone?
Your spindle provides the energy needed to cut through stone. So, stone-cutting CNC machines require very powerful spindles.
However, the power your operation draws from your spindle depends on the depth of cut and diameter of the tool.
So, shallow engravings do not require that much power.
Spindles above the 2.5 KW range should be capable of V-carving the hardest of stones at depths of around 1.5mm.
But large stone CNC machines enjoy spindles that have at least 11KW of power. They can cut thick stones.
But you should use several passes with a reasonable step down for cutting deep. For example, you can cut a stone of 6mm thickness by four passes of 1.5mm step down.
You can buy a 4KW Mophorn spindle on Amazon for a very cheap price.
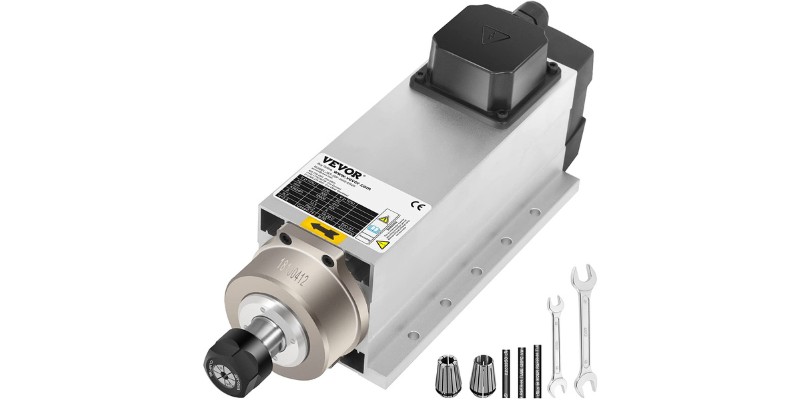
This spindle has great value for money. It is air-cooled and great for engraving stones and cutting wood and metal. You can also cut stones with it using the right step down. It provides up to 18000 RPM which is more than enough for our purposes.
And don’t worry about driving this spindle. You can also buy a Mophorn 4KW VFD for your spindle at a low price as well. This VFD can also work with your ordinary single-phase electricity.
Stepper Motors for Granite Cutting
Pushing your spindle around is also harder for stepper motors while cutting stone. So, you will need stronger stepper motors to engrave stone.
Fortunately, we are going to use low feed rates for stone engraving, and stepper motors are much stronger at lower feed rates.
So, stepper motors with holding torques in the 100Ncm (142oz.in) range should be able to keep their steps for engraving at lower feed rates, especially if you have ball screws. But if you get stronger motors you will be confident and even able to cut stones.
If you are looking for stepper motors that are cheap yet strong enough for stones, here are the most affordable ones.
If your gantry’s weight is less than 40kg, StepperOnline’s NEMA 23HS22 with 126Ncm of holding torque should be enough for you.
It is a popular stepper motor. It is also a good option for stone engraving, and it is the one of cheapest stepper motors in its torque range.
If you have a heavier CNC machine or you want a very powerful stepper motor, StepperOnline’s 23HS45 with a whopping 300Ncm has enough power for you. Once again, you get a very high holding torque for a wonderfully cheap price.
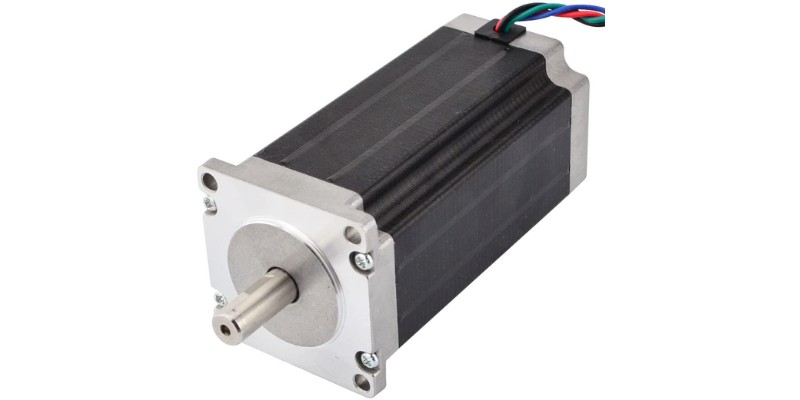
Finally, if you are looking for the cheapest stepper motors with a holding torque above 200Ncm, this stepper motor from StepperOnline is one of them. It has a high holding torque (240Ncm). But its current is a little high and it may heat up.
Feed Rate and Spindle Speed for Granite Cutting With CNC
There are a lot of considerations that can affect your choice of feeds and speeds. But as a rule of thumb, your feed rate for CNC engraving granite should be between 120 mm/min (4.7 IPM) and 800 mm/min (31.5).
Your spindle speed (RPM) should be in the range of 3000 RPM and 15000 RPM for engraving stones and granite.
To find more exact feeds and speeds consider the following information:
- If your CNC machine has rigidity problems, lower your feed rate and/or increase your RPM.
- For deeper cuts and larger tools, you need lower feed rates and lower RPMs. But for shallow engravings, you should choose higher feed rates and a higher spindle speed.
- If your spindle is not powerful enough you will need to increase your RPM and lower your feed rate.
- For softer stones like marble and limestone, use higher feed rates (and higher RPMs).
- For smaller stepovers, you should increase your feed rate.
- If you don’t have problems with rigidity, spindle power, and stepper motor power, then use trial and error: increase your feed rate and lower your spindle speed to increase your tool life. But be careful not to cause tool deflection and break your bit this way. Note that your machine’s limitations have higher priority than tool life.
You may be wondering why sometimes I tell you to change your RPM the same way you change your feed rate (for example increase both feed rate and RPM) and sometimes I tell you to go the opposite way (lower feed rate but increase RPM).
Answering that requires a deep understanding of feeds and speeds, so I can only refer you to this article.
In summary: CNC Carving Granite, Stone, and Marble
In closing, stone cutting and particularly granite cutting are difficult.
You need a very hard bit for granite engraving with a CNC machine. Diamond bits are the best choice for cutting granite and stone, but a really hard tungsten carbide bit like the Alpen Multipurpose Bit can be a cheap replacement.
A stone engraving CNC machine must have a cooling flow of water. Plus, your CNC machine should be rigid enough to stand up to the stone’s resistance.
For engraving granite with small step downs, a strong spindle and strong stepper motors can do the job. We also have explained how to decide on your feed rate and spindle speed.
So, have fun experimenting.
FAQ
Can you CNC stone?
Yes, a lot of the stones you see around you in the building are creations of CNC machines.
You can also turn your own CNC into a stone-cutting CNC if you use our tips on the right bit, rigidity, spindle power, and the correct feeds and speeds.
Can a CNC router cut stone?
Yes, the stone-cutting CNC machines have powerful spindles and have produced a lot of stones you see around you.
But you can also cut stone with your CNC machine with the right step down and right bit and a cooling system if it is rigid enough.
Can you CNC granite?
Yes, but you need a diamond bit or a tough and pure tungsten carbide bit for engraving.
You also need a rigid CNC with a cooling system. You need to set the correct feeds and speeds that take into account your machine’s ability.
Can you CNC marble?
Yes, actually it is much easier to CNC marble than to CNC granite.
If you have turned your CNC into a stone engraving CNC with our tips on rigidity, the right bit, and the cooling system, you can CNC marble without difficulty.
Check out our other CNC mill and router articles:
- The 10 best laser cutters & engravers
- The best glass laser engraving machines
- The best CNC mills 2022
- The 11 best DIY CNC routers 2022
- Best cheap CNC routers in 2022
- The complete industrial laser cutter buyer’s guide