A CNC machine can cost anywhere from a hundred couple of dollars to tens and even hundreds of thousands, depending on the type of CNC machine it is, the size and rigidity, the power and torque, number of axes, and many other factors.
Generally, this is how much each type of CNC will cost:
CNC Machine | Price |
---|---|
Hobby-Level CNC Router | $200 – $3000 |
Professional CNC Router | $3K – $10K |
Industrial CNC Router | $40K – $200K |
Production CNC Router | $200K – $400K |
Hobby-Level CNC Mill | $2K – 7K |
Professional CNC Mill | $7K – $50K |
Industrial 3-Axis Mill | $60K – $100K |
Industrial 5-Axis Mill | $200K – $500K |
Production Mill (Vertical Machining Center) | > $500K |
Hobby-Level CNC Lathe | $2K – $12K |
Professional 2-Axis CNC Lathe | $15K – $50K |
Industrial 2-Axis CNC Lathe | $60K – $100K |
Production CNC Lathe (Horizontal Machining Center With 7-13 Axes) | > $500K |
The cheapest CNC routers start at a few hundred dollars, made by popular desktop CNC brands like Sainsmart. The next step up is desktop CNCs like the X-Carve and Shapeoko machines costing a few thousand dollars, and from there, industrial machines can cost from $15K up to $1 million plus.
For more specifics, I’ll cover how much each type of CNC machine costs, including CNC routers, CNC mills, and CNC lathes as well as what features and materials each can work with.
- Factors Affecting the Price of a CNC Machine
- The Complete CNC Machine Price Guide – In Every Price Range
- The Extra Costs After You’ve Bought The CNC Machine
- Cost of Used CNC Machines
- FAQs
Factors Affecting the Price of a CNC Machine
Drive System
Hobby CNCs mostly use stepper drive systems, while industrial CNC machines have servo motors. Servo motors with industrial controllers are considerably more expensive than steppers.
Servo systems are much faster, and don’t make errors since they have closed-loop control.
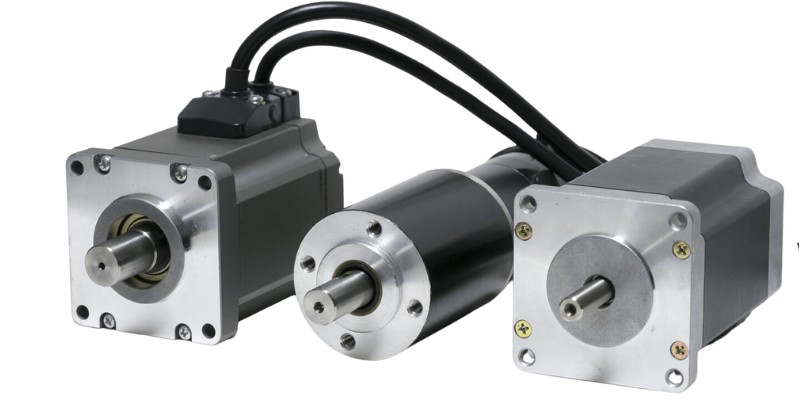
Size of the Machine (Work Envelope & Work Area)
Larger CNC machines cost far more, and large CNCs are almost always industrial machines.
For CNC routers, the work area shows the area of material you can cut with the machine. For CNC mills, the work envelope shows the volume that the mill can machine.
Number of Axes
More axes mean a more complicated and expensive CNC machine.
Conventional CNC lathes have 2 axes, and CNC mills and routers have 3 axes. 4 and 5 axes CNC machines begin to cost far more.
However, modern industrial CNCs can have up to 13 axes, but you’ll only find more than 5 axes in industrial machining centers.
Tolerance: Hobby or Industrial CNC
The most notable difference between industrial CNC machines and hobby CNCs is the tolerance of parts they can make in harder materials.
Tight tolerances need more accuracy, precision, and rigidity. For example, a hobby CNC may give 0.15mm of tolerance in a hard material, while an industrial CNC can be more than ten times as accurate (0.01mm).
Power and Speed
The power indicates the torque that the electric motors offer. This includes the main spindle, servo motors or stepper motors, other spindles (if the CNC has more), and the vacuum table if the CNC has it.
CNC Machining Center vs Ordinary CNC
CNC machining centers cost far more than standard CNCs.
CNC Machining centers are automated machinery: they have robots that fetch various tools and automatically change them (automatic tool change or ATC). These machines can mill, bore, drill, face, and do more automatically with just the computer program.
On a standard CNC, the machinist must manually stop the machine and change the tools and reset the tool offset.
The Complete CNC Machine Price Guide – In Every Price Range
Now, let’s take a more detailed look at how much is a CNC machine and what kind of specs you can get for different budgets.
HobbyCNC Prices
There are more cheap CNC machines available online than ever before. However, I still recommend to buy from trusted brands, rather than just the cheapest model available.
Reputable brands that offer low price ranges include:
- Sainsmart
- BobsCNC
- Inventables
- Carbide 3D
- Maslow CNC
- MakerMade
While everyone’s definition of “cheap” varies, we’d broadly classify a low CNC machining price as under $3,000.
Price | Machine type | Working area | Where to Buy? | |
---|---|---|---|---|
Sainsmart Genmitsu 3018 | $240 | Router | 300x180x45mm | Amazon |
BobsCNC Quantum Max | $1,580 | Router | 50.5x24x3.8” | BobsCNC website |
Shapeoko 4 XXL | $2,300 | Router | 17.5×17.5×4” | Matterhackers |
X-Carve | $2,299 | Router | 29.5×29.5×4.5” | Matterhackers |
MakerMade M2 | $1,198 | Router | 4x8ft | MakerMade website |
Nomad 3 | $2,800 | Mill | 8x8x3” | Matterhackers |
Taig Tools Micro Mill | $2,295 | Milll | 9.5×5.5×6” | Taig website |
Taig Tools M1015-5C Micro Lathe | $951 | Lathe | 8×1.75” | Taig website |
Entry-level CNC costs: under $500
You can buy entry-level CNCs for under $500.
On the lowest end of the scale, you have the likes of the Sainsmart Genmitsu 3018 PROVer, which can be picked up for as low as $240. It has a 300x180mm working area, one of the smallest sizes CNCs come in.
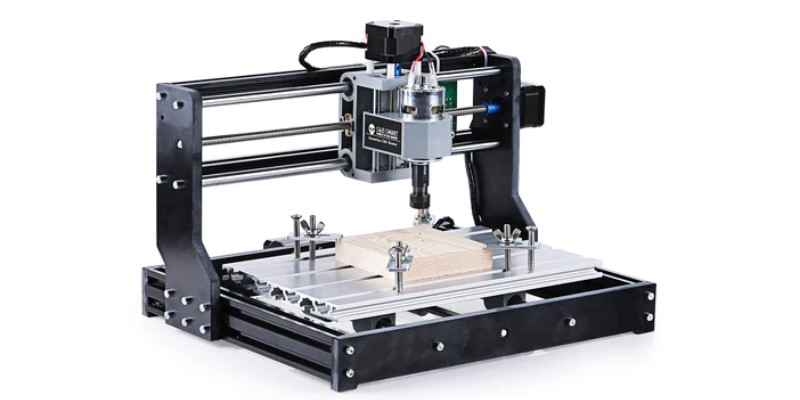
3018 CNCs are suitable for basic, non-demanding projects using materials like wood and acrylic – they aren’t very strong or precise. You can mark softer metals like aluminum with them, but it’s not recommended, and the build quality is lower quality than a more expensive machine.
Hobbyist desktop CNC price range: $500-$3000
Perhaps the two best-known and most popular budget CNCs for hobbyists are Carbide 3D’s Shapeoko 4 and Inventables X-Carve. We’ve compared the X-Carve vs Shapeoko in more depth in another article.
The Shapeoko 4 XXL retails for $2,300 and supports workpieces up to 17.5×17.5×4”, while the X-Carve costs $2,299 and has a 29.5×29.5×4” working area.
While large CNCs are generally more expensive, there are some low-cost options. For example, both the Maslow and the MakerMade M2 provide 4x8ft working areas and retail for around $600 and $1,200, respectively.
The reason these 4×8 CNCs are so cheap is that they don’t have a gantry, but this means you lose some stability and accuracy. They’re vertically mounted rather than anchored down on a sturdier table. But, they’re still fantastic for the price.
Another option for a low-cost CNC is to go for a completely DIY CNC machine. Building the machine yourself, using a kit such as those from OpenBuilds, can save you money compared to machines that come assembled – but they also require more time, effort, and technical skill to build.
Lowest-cost CNC mills: $2,000-$7,000
CNC milling machine price ranges are typically higher, but there are still some affordable models. The prices range between $2,000 and 7,000.
For example, Carbide 3D’s Nomad 3 costs $2,800 with an 8x8x3” working area. It is better for milling aluminum, brass, and copper, although you’ll need a more expensive mill to work with harder metals like stainless steel and titanium.
Taig Tools is another well-known affordable CNC mill brand, with mills such as its CNC micro mill, as well as affordable lathes, like its M1015-5C micro lathes.
However, If you’re looking to keep to a low lathe or mill cost, you’re going to be restricted to pretty small working areas.
Professional CNC Machine Cost
A professional CNC is better than a low-cost hobbyist machine. However, these machines can’t meet the tight tolerances of a machine shop or an industrial production line.
Price | Machine type | Working area | Where to Buy? | |
---|---|---|---|---|
Shapeoko 5 Pro | $3,750 | Router | 4ftx4ft | Shapeoko website |
X-Carve Pro | $9,495 | Router | 4ftx4ft | X-Carve website |
Tormach PCNC 440 | $7,010 | Mill | 10×6.25” | Tormach website |
Baileigh VM-626-1 | $6,799 | Mill | 14.5×6” | Baileigh Industrial website |
Baileigh PL-1236E | $8,148 | Lathe | 7” cutting diameter | Baileigh Industrial website |
Professional CNC routers: $3,000 to $10,000
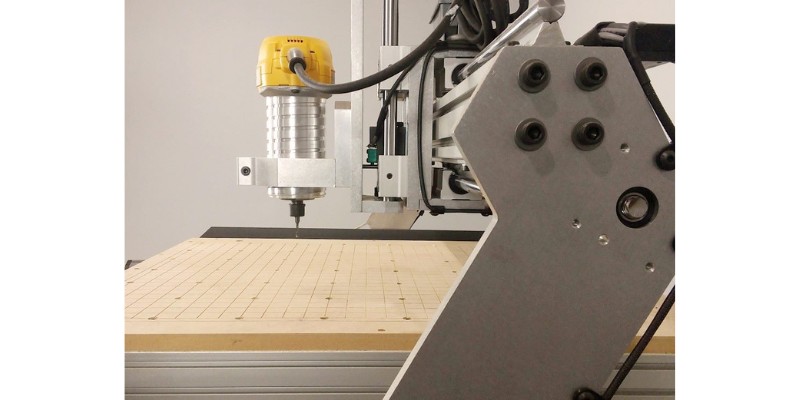
Above the $3,000 CNC router price ranges, you get to more professional models. We’re categorizing professional small business CNCs as between $3,000 and $10,000.
Professional CNCs use higher quality components, such as ballscrews for smoother, stabler and more precise axis motion than leadscrews or belt drives. You can see this in the X-Carve Pro, which has 25mm ball screws and linear guides that are accurate down to 0.01”.
More premium machines also use higher-quality steel gantries for improved rigidity. These can support more powerful routers, which can make thicker, faster cuts, and cut and carve tougher materials.
You can still use the likes of the Shapeoko 4, X-Carve, and MakerMade M2 as CNCs machines for small businesses, but more expensive CNCs offer larger working areas, more power and torque, better stability and repeatability, and more speed. Plus, they can be run for long hours, unlike cheaper CNCs.
In this price range, you can get high-quality machines with considerably larger working areas, with the typical range from around 2x2ft to 4x8ft.
Both the Shapeoko 5 Pro and X-Carve Pro come in these dimensions. The Shapeoko 5 Pro comes in 2x2ft, 2x4ft, and 4x4ft, with the largest model costing $3,750, and using significantly higher quality components. The X-Carve Pro is 4x4ft and costs significantly more at $9,495, but is a really impressive professional CNC.
Professional CNC milling machine costs: $7,000+
These professional CNC mills start at around $7,000, and are fine for startups, small shops, or serious hobbyists. But, you can’t expect a large working envelope, a powerful spindle, high-speed cutting, tight tolerances, automation, or more than 4 axes.
An example of a professional milling machine in this price range is the Tormach PCNC 440 mill entry-level package.
This starts from $7,010 and provides a 10×6.25” working area with impressive features like optional 4-axis functionality and an automatic tool changer.
Another option, with a larger 14.5×6” working area, is the Baileigh Industrial VM-626-1. It retails from $6,799 and offers a spindle speed of up to 25,000 RPM (compared to the 10,000 RPM of the cheaper Taig Micro Mill).
Industrial CNC Machine Costs
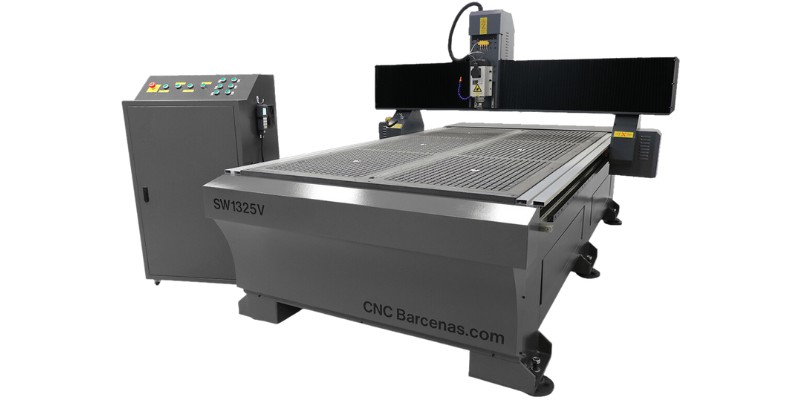
Industrial CNCs are used for production or machine shops. They are extremely accurate, powerful, fast, and have ATC and possibly more axes.
For example, they may have material infeed and have many axes for simultaneous cutting or boring.
The priciest machines are machining centers, with 7-13 axes. They have multiple spindles, automatic gearboxes that can change between the spindle and the servo on Z, and even multiple turrets and Swiss machining.
Here’s the price range for industrial CNCs:
Machine Type | Price |
---|---|
3-Axis CNC Router | $40K – $100K |
Production CNC Router (Many Axes) | $200K – $400K |
3-Axis Vertical Machining Center (Mill) | $60K – $100K |
5-Axis Mill | $200K – $500K |
Production 5-Axis Vertical Machining Center (Mill) | >$500K |
Affordable 2-Axis CNC Lathe | $15K – $50K |
High-End 2-Axis Lathe | $60K – $100K |
Horizontal Machining Center With 7 to 13 Axes | >$500K |
Some industrial CNC machine prices include:
Machine type | Working area | Where to Buy? | |
---|---|---|---|
Haas UMC-350 5 Axis | Mill | 15x14x12” | Haas website |
Haas AST-28 | Lathe | 13” cutting diameter | Haas website |
Okuma MA-400HA | Mill | 22x24x24.6” | Okuma website |
Hardinge XR | Mill | 40x24x24” | Hardinge website |
Most CNCs used in industrial production are mills and lathes, as they offer far greater stability, torque and power than CNC routers. One of the largest producers of industrial CNCs is Haas Automation, which manufactures some of the best CNC mills and CNC drilling machines.
Haas’s range of mills and lathes includes 4 and 5-axis machines, micro and large format models, and automation systems. They’re used in the making of everything from F1 cars to aerospace parts. Many Haas CNC machines cost over $100,000.
Hardinge is another brand that produces top-quality industrial CNCs, including milling, turning, drilling, and grinding machines. There are also other highly-rated brands like Mazak.
These are some of the best industrial CNC brands:
Top CNC Brands | Country |
---|---|
Mazak | Japan |
Okuma | Japan |
Haas | US |
DMG Mori | Germany |
Fadal | US |
Makino | Japan |
Matsura | Japan |
Nakamura | Japan |
Doosan | South Korea |
Vertical Machining Centers – CNC Mill Prices
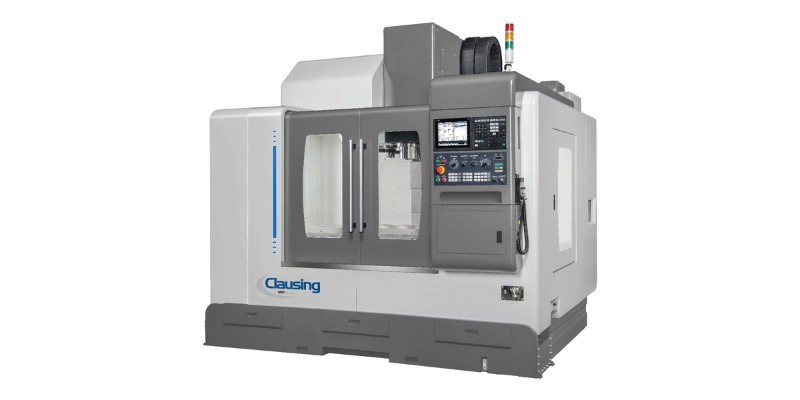
Aside from less common vertical lathes, most vertical machining centers are CNC mills. The most basic machines are 3-axis mills and cost from $50K to $100K. They are rigid enough for metalworking.
5-axis CNC machines can do 3D milling and drilling from various angles, and cost from $200K to $500K.
Production Mills
3-axis vertical production mill centers cost $200K to $500K, and 5-axis machines cost above $500K.
2-Axis CNC Lathe
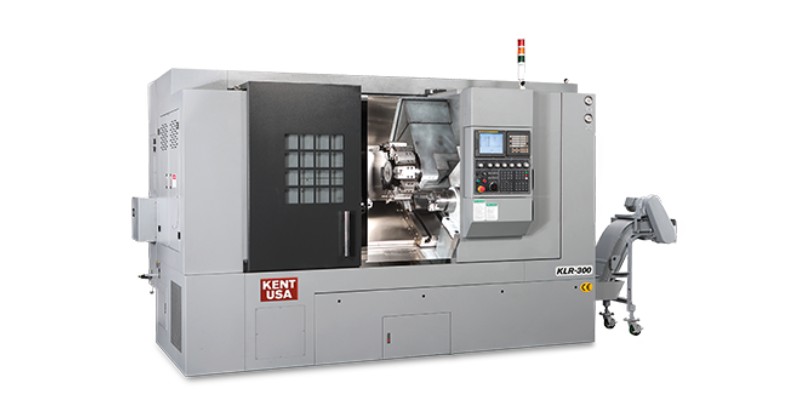
2-axis CNC lathes cost between $15K and $50K, depending on their size and power.
An industrial 2-axis CNC lathe is larger and more accurate than a standard lathe, with a more powerful spindle. It may also have a turret.
Production 2-axis Lathes
Production 2-axis CNC lathes cost between $60K and $100K.
These have added features, like automatic gearboxes for torque and speed control. You don’t have to open the headstock and change gears manually. They also have turrets that may be automatic.
Horizontal Machining Centers – CNC Turning Center Prices
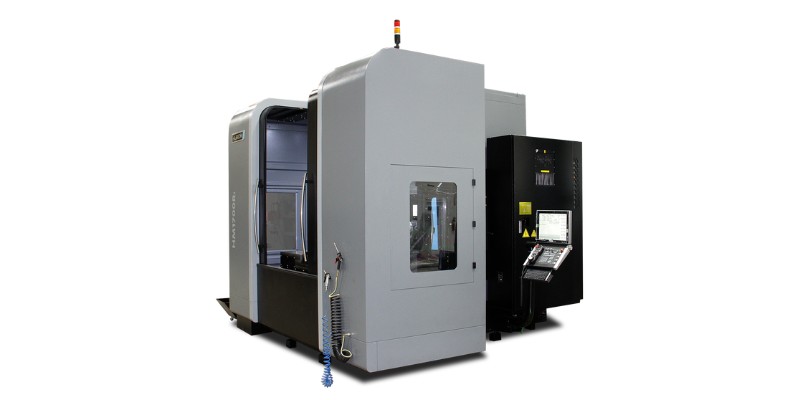
These machines are available from well-known CNC brands, and cost upwards of $500K.
Horizontal machining centers are a hybrid of lathe and mill. They’re sometimes called a “modern lathe”. These machines have many axes (often 7-13 axes), turrets, and several spindles.
- We also included a comprehensive price guide in our discussion of, “How much does a laser cutter cost?”
The Extra Costs After You’ve Bought The CNC Machine
Buying a CNC machine is just the first investment. There’s also extra equipment costs, material costs, electricity, repairs, potentially staff costs, and more.
Material Costs
CNC machine materials costs vary based on the materials you’re using. Wood is most commonly used in CNC routing, and woods like balsa are very cheap and readily available, while luxury hardwoods like mahogany are very expensive.
Here are the approximate prices for 4×8 sheets with ⅝” thickness:
Sheet | Approximate Price |
---|---|
Birch Plywood | $58 |
Sanded Cherry | $64 |
Oak Plywood | $75 |
Sanded Maple | $60 |
Sanded Pine | $40 |
If you’re using a metal CNC machine, then soft metals like aluminum are relatively cheap, while steel and titanium are more expensive.
Here’s the approximate prices for everyday metals, all in 12” lengths:
Metal | Width | Thickness | Approximate Price |
---|---|---|---|
Aluminum 6061 bar | 8” | 2” | $115 |
Aluminum 6061 sheet | 36” | 0.025” | $22 |
Aluminum 7075 bar | 5” | 2” | $170 |
Aluminum 7075 sheet | 36” | 0.032” | $22 |
Steel Round Bar | NA | 1.25” (diameter) | $17 |
Steel Round Bar | NA | 2.5” | $65 |
Steel Round Bar | NA | 3.25” | $176 |
Steel Square Bar | 1.25” | 1.25” | $30 |
Steel Square Bar | 2.5” | 2.5” | $145 |
Brass Round Bar | NA | 1.25” | $82 |
Brass Round Bar | NA | 2.5” | $240 |
Brass Square Bar | 1” | 1” | $173 |
Brass Square Bar | 2” | 2” | $680 |
Tool Costs (End Mills and Router Bits)
Below is a list of CNC tool prices. Router bits are only suitable for CNC routers processing wood or other soft materials. HSS end mills are affordable but are slower and have much less tool life. Carbide end mills are tough, long-lasting, and can handle higher cutting speeds.
Tool | Price per Piece |
---|---|
Router Bits | $1 – $3 |
HSS End Mills | $3 – $10 |
Carbide End Mills | $30 – $1200 |
Work Holding
Holding the workpiece depends on the type of CNC machine. Here are some work-holding methods in different CNCs:
- Chuck (lathe chuck holding the workpiece)
- Clamping
- Vacuum Table
For this, you need screws, vises, and edge clamps. Vises and edge clamps cost $50 to $2,000, depending on the brand and quality.
Coolant
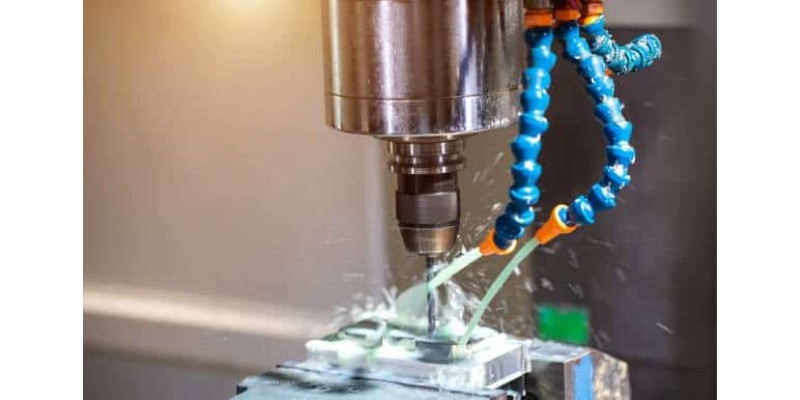
CNC machines need coolant fluid when cutting metal.
Coolant prices vary between $25 and $60 per gallon, and depend based on whether they are fully synthetic or semi-synthetic.
Repairs and upgrades
Like any machine, CNCs come with some maintenance and repair costs. Perhaps the most common is the need to replace your CNC bits, as these wear out over time, especially if subjected to demanding work.
Other components include:
Spindles
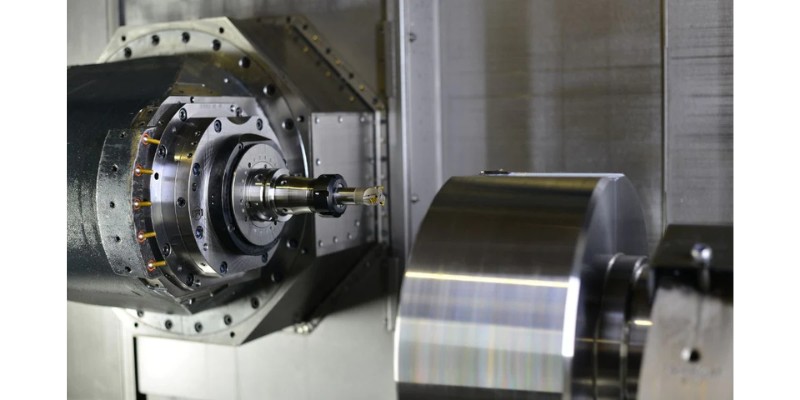
Spindles have tool lives from 6,000 to 30,000 hours depending on their quality, and how you look after them.
Costs of replacement spindles vary. Routers for hobbyists CNCs cost about $150 (for example, the Makita RT0701C), but spindles are more expensive, with cheaper Chinese air-cooled spindles by companies like Vevor costing $200-$400.
But, high-end spindles cost more. Water-cooled spindles are more expensive, and spindles with automatic tool change (ATC) are even more. Spindles with ATC compatibility cost between $1,500 and $15,000.
Stepper motors
Stepper motors have a typical tool life of around 10,000 hours, but are fairly cheap to replace. The more torque, the higher the cost.
Here’s a table for approximate stepper motor prices based on typical torques in each NEMA size.
Size | Affordable (Stepper Online) | Mid-Range (Leadshine) | High-End (Oriental Motor) |
---|---|---|---|
NEMA 17 | $10 | $15-20 | $65 |
NEMA 23 | $20 | $30 | $70-$90 |
Upgrades
Upgrade costs depends on which upgrades you want to add – and which upgrades your CNC machine can handle.
For example, one popular upgrade is to add a laser module, and these typically cost at least a few hundred dollars.
Cheap upgrades include probes to help measure the workpiece location and set the controller’s tool offset. Z-probes costs between $5 and $80. For example, XCarve’s Z-probe kit is under $30, while RATTM Motor’s Mach3 tool sensor is about $80. Other cheap upgrades include a hand controller and an HMI.
But there are more expensive upgrades for more advanced CNCs. For example, you can add a vacuum table that will grip the workpiece without clamping. If the CNC table is not compatible with vacuums, you’ll have to upgrade the table as well.
A vacuum table can cost from $5,000 to $10,000, and also affect your operational costs as they consume a lot of electricity.
Electricity cost
Generally, you can estimate around $2/hr for even a more powerful CNC machine in hourly electricity cost.
Running professional and industrial machines can cost a lot more however, and will depend on the horsepower of the motors used and the resulting wattage.
Software costs
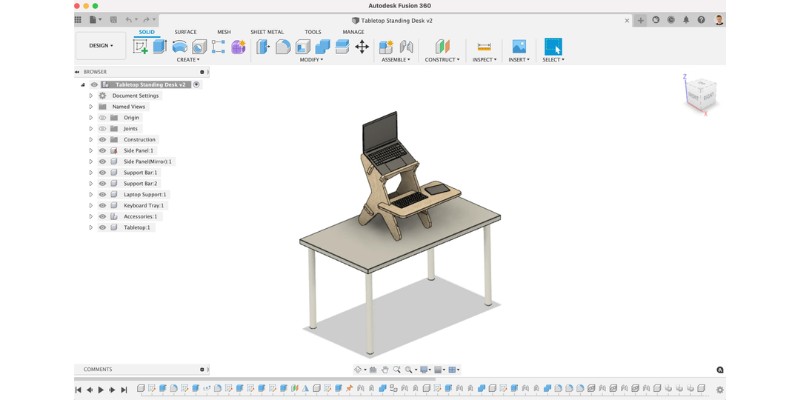
It is possible to use a CNC without paying for software. The best free CNC software include:
- Inkscape – for designing 2D vector files
- Easel Free – for design, and as a CADCAM control software
- Fusion 360 (only free for certain uses) – design and control software
- FreeCAD – free CAD design software
- GRBL Candle and Universal G-Code Sender – for control software and g-code sending
However, free CNC software can be limited in comparison to paid versions.
Some CNCs come with specific software, such as Inventables X-Carve machines and Easel, and Carbide Shapeoko machines coming with Carbide Create.
These programs can also be used with other machines, although some, software, like Makerverse for the MakerMade M2, are specialized for specific machines.
Industrial CNC brands generally provide their own custom software.
Some of the best CNC software you’ll have to pay for include the full versions of Fusion 360 for CAD/CAM, which starts from $56 monthly (alhtough it’s free for three years non-commercial use), and Mach3/Mach4 control software, which costs $200.
Finishing costs on CNC prototypes
Finishing can improve both the appearance and the durability of CNC-machined parts, and is widely used, such as on CNC prototypes.
Perhaps the cheapest finishing method is manually sanding pieces down to improve surface smoothness, and then finishing with polish or a similar product. This is commonly done for wood CNC parts. Varathane or similar products for wood cost about $30 – $50 per gallon.
A more premium option for finishing CNC products is bead blasting, also known as sand or grit blasting. Bead blasting is typically best done by a professional, and costs between $30-$45 per hour.
Another way to finish CNC products is by plating, which is used for metal products to prevent them from rusting, corroding, as well as to improve their appearance. Zinc plating costs $0.30-$0.40 per kg. Nickel, tin, and zinc are the most common and cheap plating options, with silver and gold being more expensive.
The opportunity cost of your time
If you’re starting a business, you need to add the cost of your time to your overall costs. If you could earn $25/hr working in a CNC shop, then this is the opportunity cost of your time.
And if you’re looking to start a business and want a more in-depth guide to the processes involved, I recommend you read the CNCSourced e-book on how to start a CNC business.
Cost of Used CNC Machines
A lot of people buy used industrial CNC machines since they are considerably cheaper.
However, buying a used CNC takes a lot of expertise. Don’t make the purchase without an expert’s inspection, and pay attention to the following points before buying a used CNC:
- Don’t ever buy used CNCs that aren’t sold anymore. You won’t be able to find replacement parts for them if something goes wrong. I’ve seen limited-produced spindles that will cost $80K to order a replacement.
- Major electronic problems are more problematic than major mechanical problems. This is because it’s usually difficult to find the exact electronics, especially for old models.
- Don’t buy a used CNC machine with a faulty controller. The controller alone costs above $30,000 for industrial machines.
- There are upsides and downsides to buying a less-used old machine from 2000, versus a worn-out newer model. Yes, avoid buying a worn-out 2010 CNC machine, but also consider that even less-used old machines will be slow, as they have low memory, non-existent support, and outdated controllers.
- Buy a used CNC machine with available parts and support in your area.
- Have an expert check the free play, backlash, and runout.
FAQs
How much is a CNC machine for wood?
You can pick up high-quality CNC machines for wood for anywhere between $500 to $10,000, depending on the size and power of the machine.
How much does CNC Machining cost per hour?
If you’re outsourcing CNC machining, expect to pay a minimum of $30 per hour, and up to over $100 per hour, depending on some of the following factors:
Type of machine: more professional machines will cost more.
Material: harder materials like metals take longer to machine than wood, increasing price.
Complexity of the project and how long this will take
The number of parts
Which country or area you’re in